Общие свойства
Сплавы 800H (UNS N08810) и 800HT (UNS N08811) являются материалами никеля, железа и хрома, которые устойчивы к окислению, науглероживанию и другой высокотемпературной коррозии. Химический состав двух сплавов идентичен сплаву 800 (UNS N08800), за исключением более высокого уровня углерода, присутствующего в обеих марках — (0,05–0,10%) в сплаве 800Н и (0,06–0,10%) в сплаве 800НТ. Сплав 800ХТ также имеет добавку до 1,0 % алюминия и титана. В дополнение к химическим ограничениям, оба сплава подвергаются высокотемпературному отжигу, в результате которого получается средний размер зерна ASTM 5 или крупнее. Ограниченный химический состав в сочетании с высокотемпературным отжигом обеспечивает этим материалам большую прочность на ползучесть и разрыв по сравнению со сплавом 800.
Сплав 800H обладает хорошими свойствами ползучести при температурах выше 1100 ° F (600 ° C). Он остается пластичным при длительном использовании при температурах ниже 1290 ° F (700 ° C) из-за максимального содержания титана и алюминия 0,7%. Сплав 800 со стандартным отжигом рекомендуется для эксплуатации при температуре ниже 1100 ° F (600 ° C). Сплав 800Н устойчив к восстановительным, окислительным и азотирующим атмосферам, а также атмосферам, которые чередуются между восстановительной и окислительной. Сплав остается стабильным при длительной эксплуатации при высоких температурах.
Сплав 800HT обладает превосходной силой ползучести при температурах выше 1290 ° F (700 ° C). Если применение включает в себя частые колебания температуры ниже 1290 ° F (700 ° C) или детали постоянно подвергаются воздействию температуры ниже 1290 ° F (700 ° C), следует использовать сплав 800H. Высокая термостойкость сплава 800HT сравнима со сплавом 800H. Он также остается стабильным при длительной эксплуатации при высоких температурах.
Приложений
- Химическая и нефтехимическая переработка — технологическое оборудование для производства этилена, дихлорида этилена, уксусного ангидрида, кетена, азотной кислоты и кислородного спирта
- Нефтепереработка — установки парового/углеводородного риформинга и установки гидродеалкилирования
- Выработка электроэнергии — пароперегреватели и высокотемпературные теплообменники в газоохлаждаемых ядерных реакторах, теплообменники и трубопроводные системы на угольных электростанциях.
- Приспособления для термической обработки — излучающие трубки, муфели, реторты и приспособления для термообрабатывающих печей
Стандарты
АСТМ.................. В 409АСМЕ.................. СБ 409
АМС ................... 5871
Химический анализ
Вес % (все значения максимальны, если не указано иное)
Элемент |
800Ч |
800ХТ |
Никель |
30,0 мин.-35,0 макс. |
30,0 мин.-35,0 макс. |
Хром |
19,0 мин.-23,0 макс. |
19,0 мин.-23,0 макс. |
Железо |
39.5 |
39.5 |
Углерод |
0,05 мин.-0,10 макс. |
0,06 мин.-0,10 макс. |
Марганец |
1.50 |
1.50 |
Фосфор |
0.045 |
0.045 |
Сера |
0.015 |
0.015 |
Кремний |
1.0 |
1.0 |
Алюминий |
0,15 мин.-0,60 макс. |
0,25 мин.-0,60 макс. |
Титан |
0,15 мин.-0,60 макс. |
0,25 мин.-0,60 макс. |
Алюминий и титан |
0,30 мин.-1,20 макс. |
0,85 мин.-1,20 макс. |
Физические свойства
Плотность
0,287 фунта/дюйм37,94 г/см3
Удельная теплоёмкость
32–212 °F (0,11 БТЕ/фунт-°F)460 Дж/кг-°K (0-100°C)
Модуль упругости
28.5 x 106 фунтов/кв. дюйм196,5 ГПа
Теплопроводность 200 °F (100 °C)
10,6 БТЕ/ч/фут2/фут/°F18,3 Вт/м-°K
Интервал плавления
2475 – 2525°F1357 – 1385°С
Удельное электрическое сопротивление
59,5 мкОм при 68°C99 мкОм-см при 20°C
Средний коэффициент теплового расширения |
|||
°F |
°С |
дюйм/дюйм/°F |
см/см°С |
200 |
93 |
7,9 х 10-6 |
14,4 х 10-6 |
400 |
204 |
8,8 х 10-6 |
15,9 х 10-6 |
600 |
316 |
9,0 х 10-6 |
16,2 х 10-6 |
800 |
427 |
9,2 х 10-6 |
16,5 х 10-6 |
1000 |
538 |
9,4 х 10-6 |
16,8 х 10-6 |
1200 |
649 |
9,6 х 10-6 |
17,1 х 10-6 |
1400 |
760 |
9,9 х 10-6 |
17,5 х 10-6 |
1600 |
871 |
10,2 х 10-6 |
18,0 х 10-6 |
Механические свойства
Типичные значения при 70 °F (21 °C)
Предел текучести |
Предельная прочность на растяжение |
Удлинение |
Твёрдость |
||
PSI (мин.) |
(МПа) |
PSI (мин.) |
(МПа) |
% (мин.) |
(макс.) |
29,000 |
200 |
77,000 |
531 |
52 |
126 Бринелль |
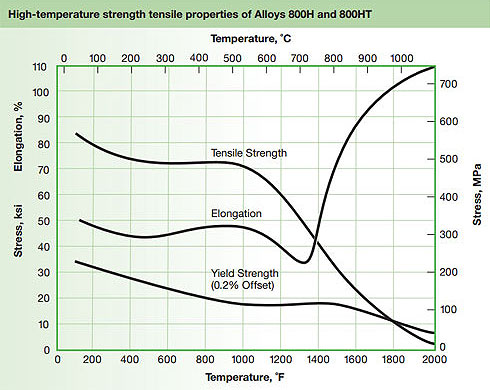
Свойства ползучести и разрыва
Строгий химический контроль и термическая обработка отжигом на твердый раствор были разработаны для обеспечения оптимальных свойств ползучести и разрыва для сплавов 800H и 800HT. В следующих таблицах подробно описаны выдающиеся свойства ползучести и разрушения этих сплавов.
Репрезентативные значения прочности на разрыв для сплавов 800H/800HT
Температура |
10 000 ч |
30 000 ч |
50 000 ч |
100 000 ч |
|||||
°F |
°С |
КСИ |
Мпа |
КСИ |
Мпа |
КСИ |
Мпа |
КСИ |
Мпа |
1200 |
650 |
17.5 |
121 |
15.0 |
103 |
14.0 |
97 |
13.0 |
90 |
1300 |
705 |
11.0 |
76 |
9.5 |
66 |
8.8 |
61 |
8.0 |
55 |
1400 |
760 |
7.3 |
50 |
6.3 |
43 |
5.8 |
40 |
5.3 |
37 |
1500 |
815 |
5.2 |
36 |
4.4 |
30 |
4.1 |
28 |
3.7 |
26 |
1600 |
870 |
3.5 |
24 |
3.0 |
21 |
2.8 |
19 |
2.5 |
17 |
1700 |
925 |
1.9 |
13 |
1.6 |
11 |
1.4 |
10 |
1.2 |
8.3 |
1800 |
980 |
1.2 |
8.3 |
1.0 |
6.9 |
0.9 |
6.2 |
0.8 |
5.5 |
Стойкость к окислению
Сочетание высокого содержания никеля и хрома в сплавах 800Н и 800НТ обеспечивает отличную стойкость к окислению обоих сплавов. Результаты испытаний на циклическое окисление при температурах 1800 °F (980 °C) и 2000 °F (1095 °C) показаны ниже.
Коррозионная стойкость
Высокое содержание никеля и хрома в сплавах 800H и 800HT обычно означает, что они будут иметь очень схожую коррозионную стойкость в водной среде. Сплавы обладают коррозионной стойкостью, сравнимой с 304 при использовании в азотных и органических кислотах. Сплавы не должны использоваться в серной кислоте. Они подвержены осаждению карбида хрома при длительной эксплуатации в диапазоне температур 1000–1400 °F (538–760 °C).
Поскольку сплавы 800H и 800HT были разработаны в первую очередь для высокотемпературной прочности, коррозионные среды, воздействию которых подвергаются эти марки, обычно включают высокотемпературные реакции, такие как окисление и цементация.
Производственные данные
Сплавы 800H и 800HT легко свариваются и обрабатываются стандартными методами производства. Однако из-за высокой прочности сплавов они требуют более мощного технологического оборудования, чем стандартные аустенитные нержавеющие стали.
Горячая формовка
Диапазон температур горячей обработки для сплавов 800H и 800HT составляет 1740–2190 °F (950–1200 °C), если деформация составляет 5 процентов или более. Если степень горячей деформации составляет менее 5 процентов, рекомендуется диапазон температур горячей обработки от 1560 до 1920 °F (850–1050 °C). Если температура горячего обрабатываемого металла падает ниже минимальной рабочей температуры, деталь необходимо повторно нагреть. Сплавы должны быть закалены водой или быстро охлаждены на воздухе в диапазоне температур 1000–1400 °F (540–760 °C). Сплавы 800Н и 800НТ требуют отжига на твердый раствор после горячей обработки для обеспечения оптимального сопротивления ползучести и свойств.
Холодная штамповка
Сплавы должны находиться в отожженном состоянии до холодной штамповки. Скорость деформационного упрочнения выше, чем у аустенитных нержавеющих сталей. Это следует учитывать при подборе технологического оборудования. Промежуточная термическая обработка может потребоваться при высокой степени холодной обработки или при деформации более 10 процентов.
Сварка
Сплавы 800H и 800HT можно легко сваривать большинством стандартных процессов, включая GTAW (TIG), PLASMA, GMAW (MIG/MAG) и SMAW (MMA). Материал должен находиться в отожженном растворе состоянии, без смазки, маркировки или окалины. Термическая обработка после сварки не требуется. Чистка щеткой из нержавеющей стали после сварки удалит тепловой оттенок и создаст площадь поверхности, не требующую дополнительного травления.
Обработки
Сплавы 800Н и 800НТ предпочтительно обрабатывать в отожженном состоянии. Поскольку сплавы склонны к деформационному упрочнению, следует использовать только низкие скорости резания и постоянно использовать режущий инструмент. Достаточная глубина резания необходима для того, чтобы избежать контакта с ранее сформированной зоной нагартованного пропила.